What are the factors affecting the quality of rubber soft joint products?
May-23-18
What are the factors affecting the quality of rubber soft joint products?
With the continuous promotion of the urban modernization process, the demand for rubber soft joints continues to rise, and customers who purchase rubber soft joint equipment also continue to rise, based on customer feedback response found that the product rubber soft joints common phenomenon three problems, this problem seriously affects the quality. Rubber joint round ball in the production, the processing process is very large level seriously affects the quality of rubber joints, rubber joints shrinkage occurs, what are the reasons caused by it, today we will understand.
First, plastic molds; multiple inlet molds need to adjust the mold filling rate of each inlet, symmetry to set up the inlet. Single ball rubber joint mold parts should be effectively set up cooling circulation waterway, to ensure that the mold cooling to remove or reduce shrinkage to play a good effect. All abrasives should be free of burrs and have mold locking tightness, able to withstand high pressure, fast, low viscosity melt filling.
Second, injection molding equipment; not enough feeding, injection molding machine screw or plunger pump bias grinding, injection and test pressure melt leakage, reducing the amount of mold filling pressure ash, resulting in insufficient melt. The nozzle hole is too big or too small. Too small will be easy to block the inlet channel, very large will lead to injection force is not large, filling the mold to produce difficult.
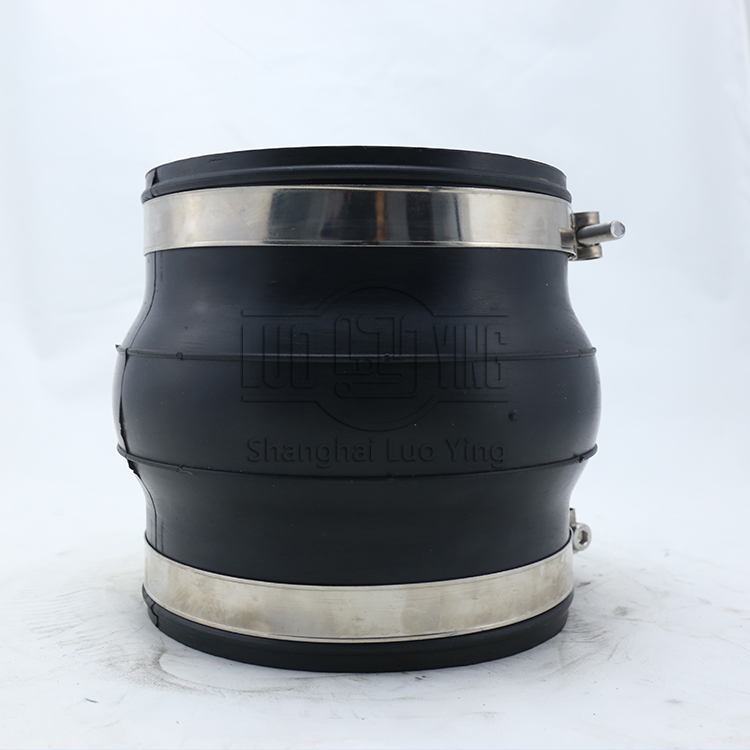
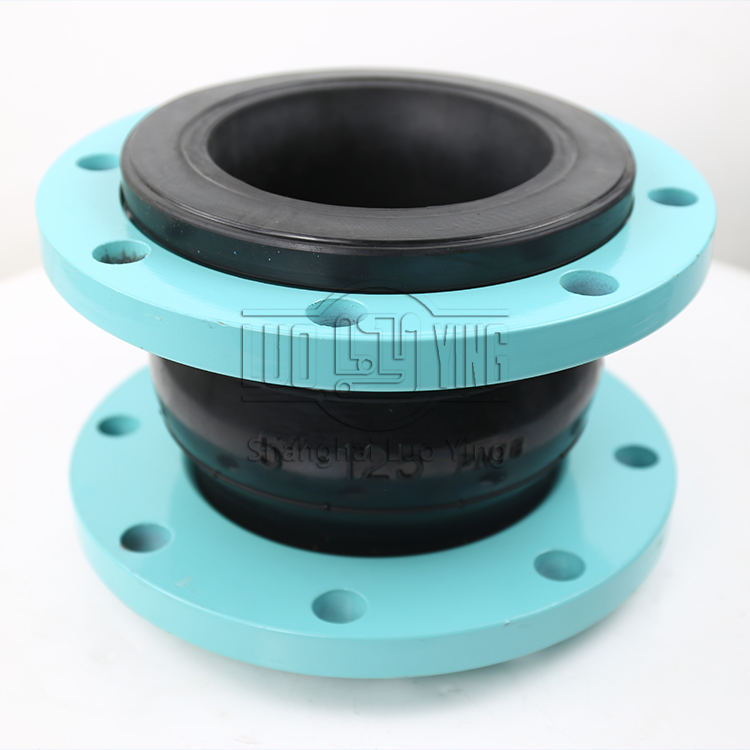
Third, the production process; enhance the injection work pressure, test pressure work pressure, increase the injection time. For personnel mobility plastic, Kor pressure will also produce burrs cause collapse pit should be properly adjusted material temperature, down the front of the barrel and nozzle temperature, so that the melt into the concave mold capacity shift is reduced, easy to cold solidification; for high viscosity plastic, the barrel temperature should be raised, so that filling the mold is very easy. Shrinkage appears in the area of the inlet to increase the holding time. Increase the injection rate can be easier to make the parts filled with and remove most of the shrinkage. For thick-walled parts, increase the abrasive temperature to ensure smooth material flow; for thick-walled parts, lower the mold temperature to speed up the drying of the outer skin. Increase the cooling time of the parts in the structure, maintain uniform production time, increase the back pressure type, and keep a certain amount of shock absorbing rubber pad at the front of the screw, etc. are beneficial to reduce the shrinkage. Low-precision products should be demolded as early as possible so that the air or boiling water slowly dissipate heat, can make shrinkage dents gently also does not affect the application.
Fourth, the raw material problem: the raw material is too soft and easy to dent, an effective way to add nucleating agent in the single ball rubber joint injection molding process to accelerate the crystallization.