What is the cause of foaming in the use of rubber flexible connections?
May-23-19
What is the cause of foaming in the use of rubber flexible connections?
The phenomenon of foaming rubber flexible connections is a very common phenomenon in the process of use, but also many manufacturers do not pay much attention to the problem. Many manufacturers believe that foaming is not a leak, not a quality problem. In fact, this idea is wrong. The most fundamental reason for blistering is the problem of quality accidents when processing rubber flexible connections.
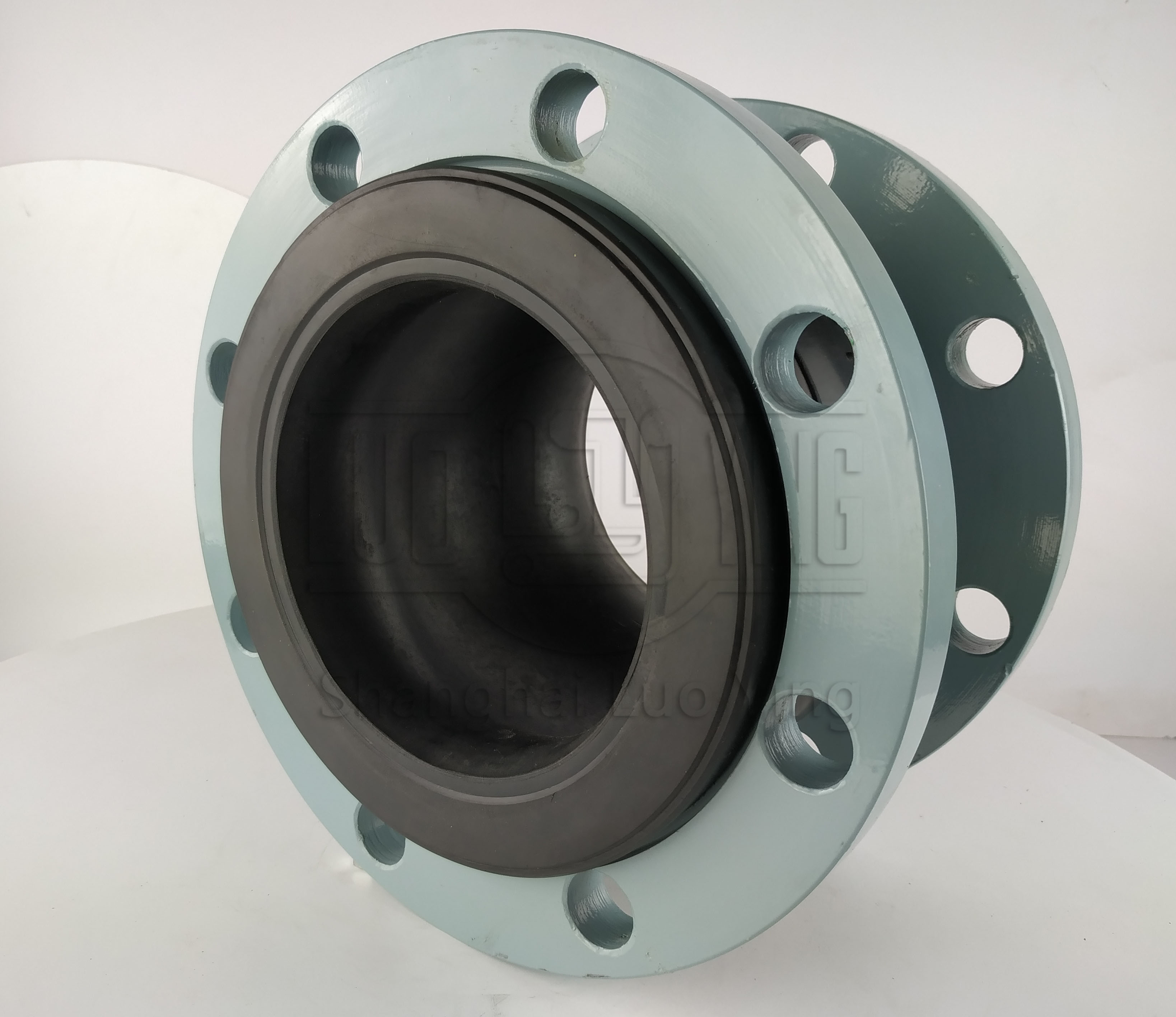
Here we will look at the real causes of rubber flexible connections blistering: 1, the quality of the foaming agent (1) check whether the foaming agent within the limited period of time, whether qualified (2) the plasticity of rubber. 2, check whether the plasticity of the rubber is up to standard, if the plasticity is too low, you should make up the mix, increase the plasticity to facilitate the generation of pores; 3, mixing temperature is too high, the foaming agent will be decomposed in advance, check the dense refining machine discharge Check whether the temperature is too high, whether the roller temperature is too high, and whether the rubber is burnt. Some rubber mixing temperature is high, you can mix a small amount or add foam rework; 4, the rubber storage time is too long or storage temperature is too high, part of the foam volatilization or decomposition, rubber storage time is too long 5, the rubber vulcanization speed is too fast: adjust the formula, check whether the critical temperature of the vulcanizing agent is close to the decomposition temperature of the foaming agent, coordinate with each other, so that the vulcanization speed matches the foaming speed; 6, the pressure is too high, more than the foaming agent The internal pressure formed by the gas produced, resulting in insufficient foaming holes; adjust the machine pressure.