How to maintain the external pressure corrugated compensator in the strong acid and alkali environme
Jul-23-07
How to maintain the external pressure corrugated compensator in the strong acid and alkali environment to extend the life?Maintaining the external pressure corrugated compensator in a strong acid and alkali environment requires careful attention to certain key areas to ensure its longevity. Here are some measures that can be taken to extend the life of the compensator:
1 . Material selection: The choice of materials for the compensator is crucial when dealing with strong acids and alkalis. It is essential to select corrosion-resistant materials that can withstand the chemical environment. Commonly used materials include stainless steel, Hastelloy, and PTFE (polytetrafluoroethylene). Consider consulting with a materials engineer or corrosion expert to identify the most suitable materials for your specific application.
2 . Proper installation: Correct installation is vital to ensure the compensator functions optimally and remains durable. Make sure all bolts, clamps, and connectors are properly tightened and aligned. Improper installation can lead to stress concentrations or uneven loading, which can accelerate corrosion and reduce the compensator's lifespan.
3 . Regular inspection and maintenance: Regular inspection of the compensator is crucial for identifying any signs of damage or corrosion. Inspect for leaks, cracks, deformation, or any other visible damage. Additionally, check the integrity of seals, gaskets, and flanges. Carry out maintenance procedures as recommended by the manufacturer or based on the compensator's specific operating conditions.
4 . Cleaning and flushing: Cleaning the compensator periodically will help remove any built-up deposits or contaminants that may contribute to corrosion. Flushing the compensator with a suitable cleaning solution or a dilute acid/alkali solution can help remove scale or sludge accumulation. Always follow proper safety protocols and ensure proper disposal of any chemicals used during cleaning.
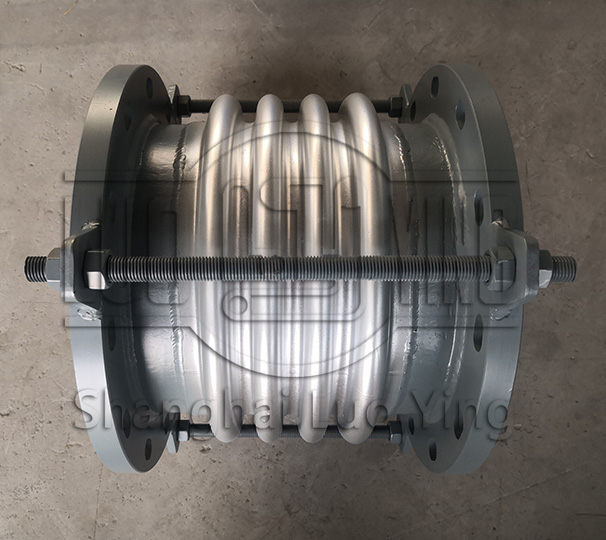
6 . Protective coatings and liners: Applying protective coatings or liners to the external surface of the compensator can provide an extra layer of protection against acid and alkali corrosion. Polyethylene or epoxy coatings can be used to shield the compensator from the corrosive environment. Ensure that the chosen coating is compatible with the compensator's material and the operating conditions.
7 . pH regulation: Maintaining the pH of the acid or alkali solution within the designed range can help reduce the corrosive effects on the compensator. Monitoring and controlling the pH through appropriate chemical additives or pH regulators can mitigate the corrosive impact on the compensator.
8 . Avoiding mechanical stress and vibration: Excessive mechanical stress, vibrations, or movements can lead to premature failure of the compensator. Minimize or eliminate potential sources of stress or vibration near the compensator. Consider using additional supports or vibration dampeners if necessary.
9 . Training and awareness: Ensure that personnel working with the compensator are adequately trained in its handling, installation, and maintenance. They should be aware of the specific requirements and precautions for working in strong acid and alkali environments.
In summary, maintaining an external pressure corrugated compensator in a strong acid and alkali environment requires careful material selection, proper installation, regular inspection, cleaning, temperature and pressure monitoring, protective coatings, pH regulation, minimizing stress and vibration, and appropriate training and awareness. Implementing these measures will help extend the life of the compensator and ensure its efficient operation in such challenging environments.