Quality control of detachable expansion joints.
Aug-23-01
Quality control of detachable expansion joints.Quality control is essential when it comes to detachable expansion joints. These joints, also known as dismantleable or dismantling joints, are critical components in piping systems, providing flexibility and ease of maintenance. In this article, we will discuss the importance of quality control in detachable expansion joints, including the key parameters to consider, testing procedures, and industry standards.
The first aspect of quality control for detachable expansion joints is ensuring accurate dimensional and fabrication specifications. These joints are assembled and disassembled during maintenance or repair activities. Therefore, precise dimensions of each component, such as the body, flanges, bolts, and gaskets, are crucial for proper alignment and connection. Deviations from the specified dimensions can lead to potential leaks, misalignment, or failure of the joint. It is vital to ensure that the manufacturing process adheres to the required dimensional tolerances to maintain the integrity of the joint.
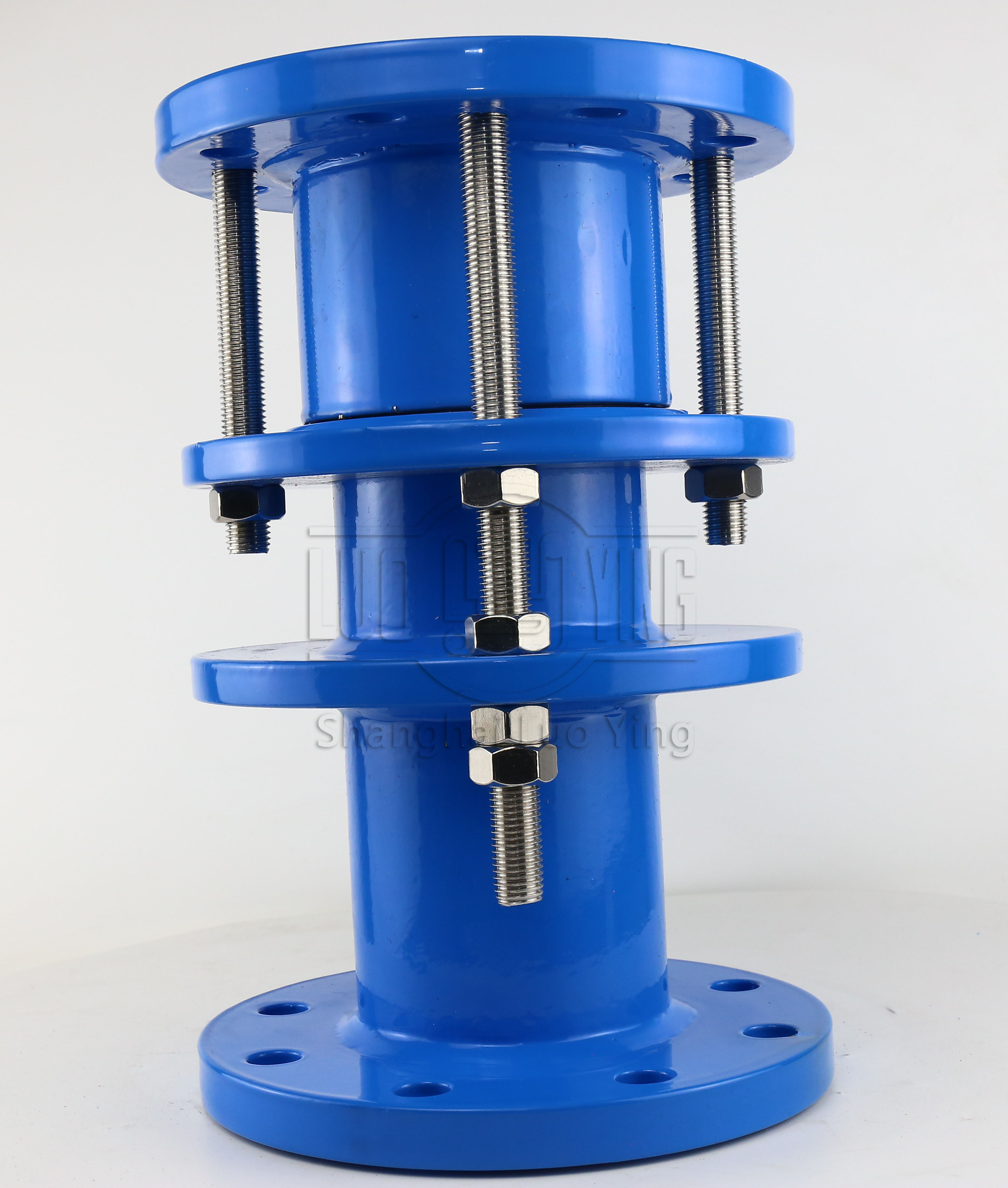
The welding and assembly processes used in manufacturing detachable expansion joints require stringent quality control measures. Proper weld quality and joint integrity are crucial to ensure the durability and reliability of the joint. Welding procedures should be qualified, and welders should be certified to perform the required welding techniques. Quality control measures, such as weld visual inspection, ultrasonic testing, or radiographic examination, should be implemented to detect any defects or discontinuities in the welds. Additionally, assembly procedures should be followed meticulously to ensure the correct alignment and connection of the joint components.
Testing plays a vital role in quality control for detachable expansion joints. Hydrostatic pressure testing is commonly performed to validate the strength and integrity of the joint. This involves subjecting the joint to a specified pressure level, typically higher than the operating pressure, and examining for any leaks or deformations. Additional tests, such as cycle life testing or fatigue testing, may be performed to assess the joint's performance under repetitive loading conditions. These tests provide valuable data on the ability of the joint to withstand the intended movements and operating conditions.
To ensure consistent quality, there are industry standards and specifications that provide guidelines for the design, manufacturing, testing, and performance of detachable expansion joints. Examples of such standards include the American National Standards Institute (ANSI) and the American Society of Mechanical Engineers (ASME) standards. Following these standards ensures that the detachable expansion joints meet the necessary requirements for quality, safety, and performance.
In conclusion, quality control is paramount in the manufacturing and testing of detachable expansion joints. Proper dimensional specifications, material selection, welding and assembly processes, and thorough testing contribute to the overall quality and reliability of these joints. Adhering to industry standards and conducting rigorous quality control procedures ensures that the detachable expansion joints meet the necessary requirements and provide the desired flexibility and ease of maintenance in piping systems.