Four Molding Processes for Restricted Steel Expanders.
Aug-23-28
Four Molding Processes for Restricted Steel Expanders. Restricted steel expanders, also known as restrained steel expanders, are critical components used in various industries, including oil and gas, aerospace, automotive, and manufacturing. These expanders are designed to increase the diameter of pipes or tubes, creating a tight seal and ensuring optimal performance in piping systems. In order to manufacture high-quality restricted steel expanders, several molding processes are utilized. Here, we will discuss four common molding processes used for manufacturing restricted steel expanders.
Sand Casting: Sand casting is a widely used molding process for producing restricted steel expanders. In this process, a pattern of the desired expander shape is created using a mixture of sand and a bonding agent. The sand mixture is packed around the pattern, creating a mold cavity. Molten steel is then poured into the mold, filling the cavity. After solidification, the sand mold is broken away, revealing the finished expander. Sand casting allows for the production of complex shapes and is suitable for both small-scale and large-scale production.
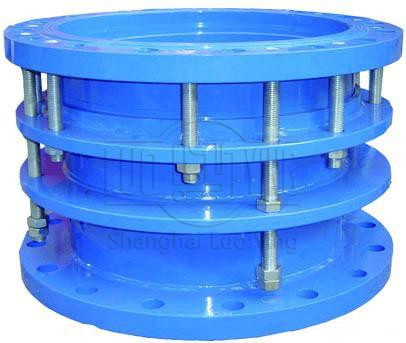
Die Casting: Die casting is a molding process commonly used for producing restricted steel expanders with high dimensional accuracy and surface finish. In this process, a steel mold, called a die, is created with the desired expander shape. Molten steel is then injected into the die under high pressure, filling the cavity. The steel solidifies quickly, and the die is opened to extract the finished expander. Die casting offers excellent repeatability and is suitable for high-volume production of expanders with consistent dimensions and quality.
Powder Metallurgy: Powder metallurgy is a molding process that involves compacting metal powders into the desired shape and then sintering them to form a solid piece. In the case of restricted steel expanders, metal powders with specific compositions and properties are selected and mixed thoroughly. The powder mixture is then compacted into a die under high pressure, creating a green compact. The green compact is then sintered at high temperatures, causing the particles to bond together, resulting in a dense and solid expander. Powder metallurgy offers good control over material properties and can produce complex shapes with precise dimensional accuracy.
These four molding processes play a significant role in the manufacture of restricted steel expanders. Each process has its own advantages and is suitable for different production volumes, expander designs, and material requirements. Manufacturers carefully select the appropriate molding process based on factors such as cost-effectiveness, quality requirements, and the complexity of the expander design. By utilizing these molding processes, high-quality restricted steel expanders can be produced to meet the demanding needs of various industries.