The production process of corrugated expansion joints is explained specifically.
Sep-23-02
The production process of corrugated expansion joints is explained specifically. Corrugated expansion joints play a crucial role in accommodating the movement and thermal expansion of pipelines, ducts, and other systems. In this article, we will specifically delve into the production process of corrugated expansion joints, highlighting the key steps involved and the materials used.
Design and Engineering: The production process starts with the design and engineering phase. During this stage, engineers determine the specific requirements of the expansion joint, such as its size, operating conditions, movement capabilities, and pressure ratings. This information is used to create detailed design drawings and specifications.
Material Selection: The selection of materials is crucial in ensuring the expansion joint's performance and longevity. Common materials used for corrugated expansion joints include stainless steel, carbon steel, or other alloys. These materials are chosen for their corrosion resistance, durability, and ability to withstand high temperatures and pressures.
Metal Forming: The next step in the production process is metal forming. Sheets of the selected material are fed into a specialized machine that corrugates them, forming the characteristic waves or ridges. The corrugations provide flexibility and allow for expansion and contraction of the joint. The depth, pitch, and shape of the corrugations are carefully controlled to meet the design requirements.
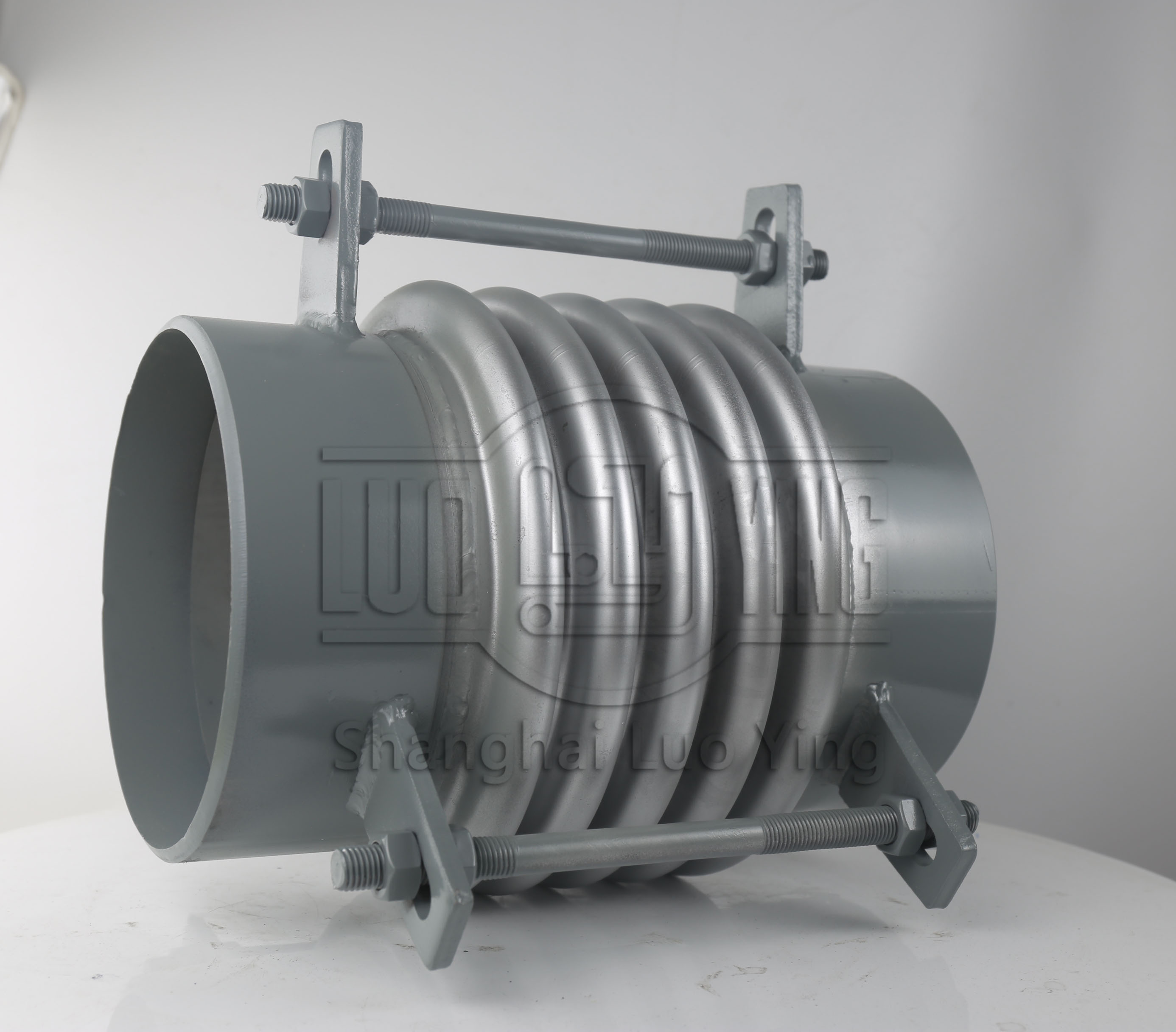
Reinforcement and Supports: To enhance the strength and stability of the expansion joint, additional reinforcement and supports may be incorporated. This can include the addition of flanges or tie rods along the ends of the joint, depending on the application requirements. These reinforcements help to distribute forces and reduce stress concentrations, improving the overall performance of the expansion joint.
Surface Treatment: After fabrication, the expansion joint undergoes surface treatment processes. This can include processes such as pickling, passivation, or coating, which are applied to protect against corrosion and increase the joint's longevity. Surface treatments also provide an aesthetically appealing finish and ensure the joint's compatibility with the surrounding environment.
Testing and Quality Control: Once the expansion joint is manufactured, it undergoes rigorous testing and quality control inspections. Non-destructive testing techniques, such as pressure testing and visual inspections, are conducted to verify the joint's performance, leak tightness, and overall compliance with the design specifications. These tests ensure that the expansion joint meets the required safety standards and reliability.
Packaging and Delivery: Finally, the expansion joints are individually packaged and prepared for shipment to their respective destinations. Proper packaging and handling procedures are followed to protect the joints during transportation and ensure they arrive in optimal condition.
In conclusion, the production process of corrugated expansion joints involves several key steps, including design and engineering, material selection, metal forming, welding and fabrication, reinforcement and support incorporation, surface treatment, testing and quality control, and packaging and delivery. By following these steps, manufacturers can produce high-quality expansion joints that can effectively accommodate movement and thermal expansion in various applications.