Metal corrugated compensator classification, specification.
Oct-23-17
Metal corrugated compensator classification, specification.Metal corrugated compensators, also known as expansion joints or expansion compensators, are vital components used in piping systems to absorb movement, compensate for thermal expansion and contraction, and reduce stress. These compensators are constructed using metal corrugated elements and come in different classifications and specifications. In this article, we will explore the classification and specifications of metal corrugated compensators.
Classification:
Metal corrugated compensators can be classified based on several factors, including their design, construction, and application requirements. Below are some common classifications:
Axial Expansion Joints: Axial compensators are designed to accommodate axial movement along the pipe axis. They consist of metal corrugations that allow for expansion and contraction in a linear direction. These compensators are widely used in applications where the primary movement occurs along the pipe axis.
Lateral Expansion Joints: Lateral compensators are designed to accommodate lateral movement perpendicular to the pipe axis. They feature metal corrugations that provide flexibility for movements occurring in a transverse direction. These compensators are useful in applications where pipes need to accommodate lateral shifts or movements.
Angular Expansion Joints: Angular compensators are designed to absorb angular deflection or rotation around a single plane. They consist of metal corrugations that allow for rotational movement. These compensators are suitable for applications where pipes experience angular movements due to thermal expansion or external forces.
Universal Expansion Joints: Universal compensators are designed to accommodate multi-directional movement, including axial, lateral, and angular movements. They combine axial, lateral, and angular corrugations to provide flexibility in multiple directions. These compensators are used in applications where pipes experience complex movements or where the direction of movement is unpredictable.
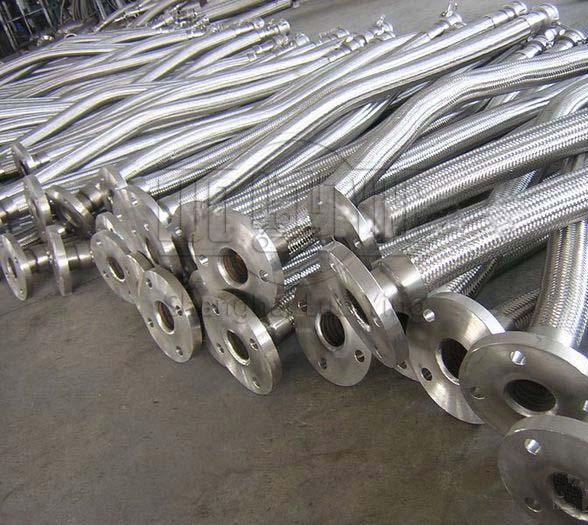
Metal corrugated compensators come in various specifications to meet different application requirements. Some important specifications to consider when selecting a compensator include:
Size Range: Compensators are available in a range of sizes to suit different pipe diameters and system requirements. The size range determines the maximum and minimum axial, lateral, or angular movements that can be accommodated.
Material: Metal corrugated compensators can be manufactured using different materials based on the application's temperature, pressure, and medium. Common materials include stainless steel, carbon steel, and other alloy steels that offer good strength and corrosion resistance.
Pressure Rating: Compensators are designed to withstand specific pressure levels based on the system requirements. The pressure rating indicates the maximum pressure the compensator can safely handle without failure.
Temperature Range: The temperature range specifies the minimum and maximum temperatures within which the compensator can operate effectively without thermal degradation or failure.
End Connections: Compensators come with different end connections, such as flanged, threaded, or welded ends, to facilitate proper installation and connection to the piping system.
Movement Capacity: The movement capacity of a compensator refers to its ability to accommodate axial, lateral, and angular movements. It is essential to select a compensator with sufficient movement capacity to meet the specific system requirements.
In conclusion, metal corrugated compensators are crucial for managing movement, thermal expansion, and contraction in piping systems. They can be classified into axial, lateral, angular, and universal types based on their design and movement characteristics. When selecting a compensator, specifications such as size range, material, pressure rating, temperature range, end connections, and movement capacity should be considered to ensure proper and efficient operation in the intended application.