Explanation of material requirements for PTFE compensators.
Oct-23-21
Explanation of material requirements for PTFE compensators.PTFE (Polytetrafluoroethylene) compensators, also known as expansion joints or bellows, are widely used in various industrial applications, including chemical processing, pharmaceuticals, food processing, power generation, and petrochemical industries. These compensators are designed to absorb thermal expansion, vibration, and movement in piping systems, ensuring the system's integrity and preventing structural damage. Understanding the material requirements for PTFE compensators is crucial to ensure their reliable performance. This article will discuss the key aspects to consider when selecting materials for PTFE compensators.
Temperature Resistance: PTFE compensators are exposed to a wide temperature range in various applications. The material should possess excellent temperature resistance to withstand both high and low temperatures without undergoing deformation or damage. PTFE, being a fluoropolymer, exhibits exceptional thermal stability, allowing it to withstand temperatures ranging from -200°C to +260°C.
Chemical Resistance: PTFE compensators come into contact with a wide range of corrosive and aggressive chemicals. The material must have exceptional chemical resistance to ensure longevity and prevent degradation. PTFE is known for its outstanding chemical resistance, making it resistant to acids, alkalis, solvents, and many other aggressive chemicals. It is resistant to attack from nearly all chemicals, except certain fluorinated compounds and molten alkali metals.
Pressure Rating: PTFE compensators should be able to withstand the pressure conditions in the piping system. The pressure rating of the compensator should align with the system's maximum pressure, including pressure surges and fluctuations. PTFE, being a robust and durable material, exhibits excellent pressure resistance properties, making it suitable for high-pressure applications.
Flexibility and Movement: PTFE compensators should have sufficient flexibility and movement capacity to accommodate axial, lateral, angular, and torsional movements in the piping system. PTFE possesses good flexibility and can absorb these movements without compromising its structural integrity. It exhibits low spring rate characteristics, allowing it to absorb large amounts of movement.
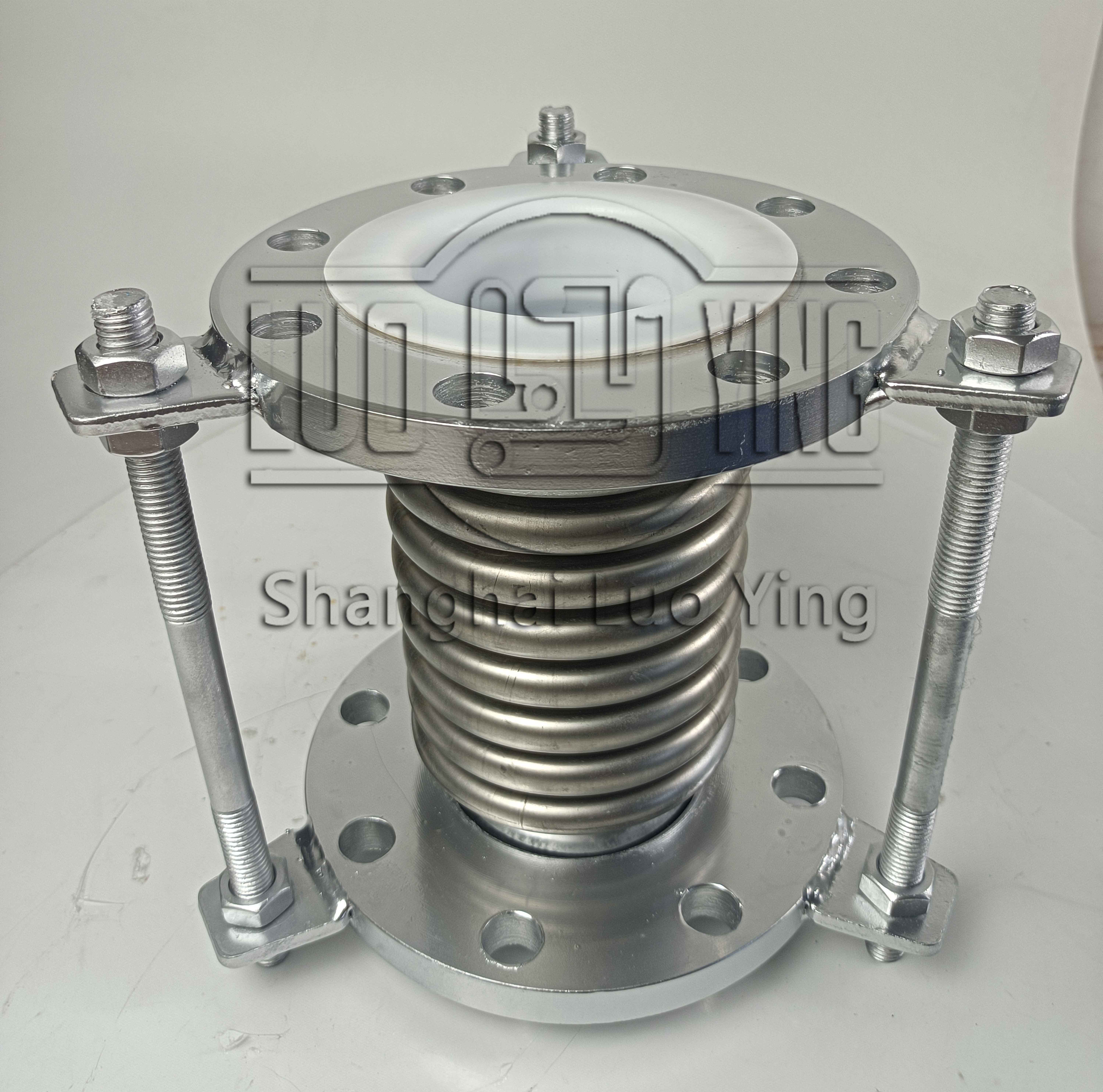
Electrical Insulation: PTFE is an excellent electrical insulator, which makes it suitable for applications requiring electrical insulation. It maintains its electrical properties even at high temperatures, making it useful in electrical and high-voltage applications.
FDA Compliance: In industries where PTFE compensators come into contact with food or pharmaceutical products, compliance with FDA regulations is essential. PTFE is often compliant with FDA regulations, making it suitable for use in food processing, pharmaceuticals, and other related applications.
In summary, PTFE compensators require materials that exhibit exceptional temperature resistance, chemical resistance, pressure resistance, flexibility, non-stick properties, electrical insulation, and compliance with FDA regulations. PTFE, with its unique properties, fulfills these requirements and makes it a popular choice for compensator applications. However, when selecting PTFE materials, it is important to consider specific application requirements and consult experienced engineers or manufacturers to ensure optimal performance and longevity of the compensators.