Rubber compensators are mainly used to compensate for straight pipelines.
Oct-23-24
Rubber compensators are mainly used to compensate for straight pipelines.Rubber compensators, also known as expansion joints, are commonly used in various industries to compensate for thermal expansion, contraction, and misalignment in straight pipelines. These flexible connectors are designed to absorb movements and vibrations, ensuring the integrity and functionality of the pipeline system. In this article, we will explore the main applications of rubber compensators in straight pipelines and provide some guidelines for their proper use and maintenance.
Understanding the Purpose: Rubber compensators are primarily used to compensate for thermal expansion and contraction in straight pipelines. As temperature changes, pipelines expand or contract, which can lead to stress and potential damage. Rubber compensators absorb these movements and mitigate the impact on the pipeline and its connected equipment.
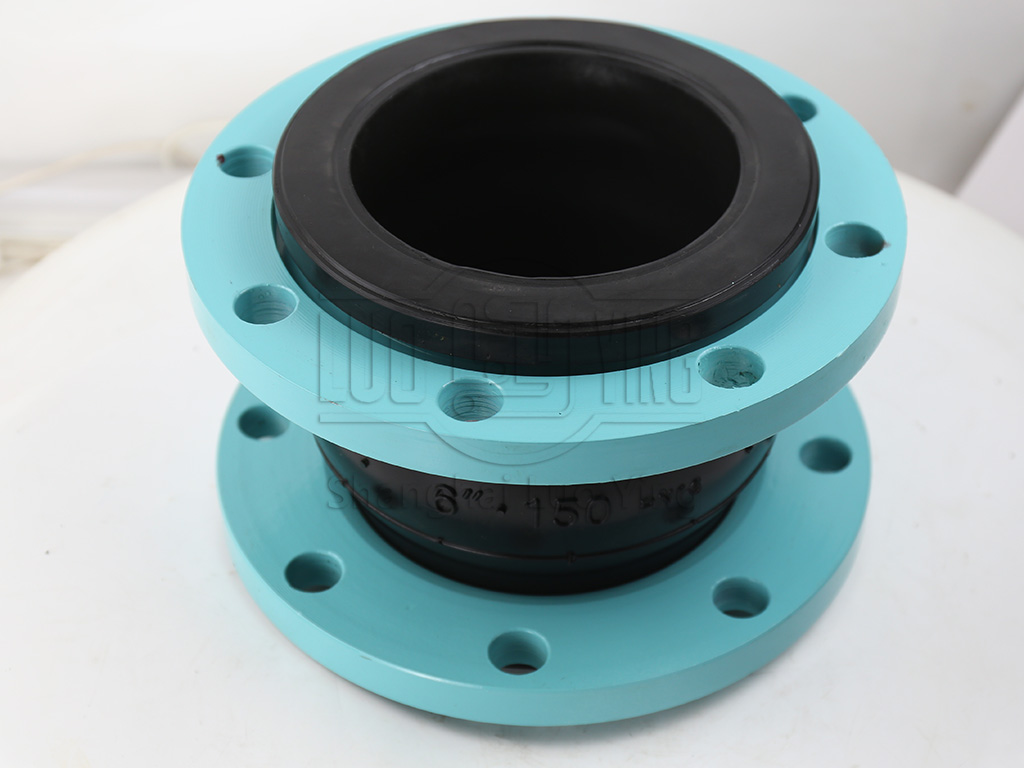
Axial compensators: These compensators are designed to absorb axial movements along the pipe's longitudinal axis.
Lateral compensators: They compensate for lateral movements, allowing the pipe to move horizontally.
Angular compensators: Designed to absorb angular movements, these compensators accommodate rotations or bends in the pipe system.
Proper Installation: When installing rubber compensators, consider the following guidelines:
Determine proper placement: Analyze the pipeline system to identify the suitable locations for installing compensators based on temperature fluctuations and movement characteristics.
Ensure correct alignment: Align the compensator's ends with the flanges of the pipeline, ensuring a secure and leak-proof connection.
Proper support and bracing: Provide adequate support and bracing to prevent excessive stress or movement that could damage the compensator or the pipeline system.
Avoid excessive heat exposure: Protect the rubber compensator from excessive heat sources or direct contact with hot surfaces to prevent premature aging or damage.
Maintenance and Monitoring: To maximize the lifespan and effectiveness of rubber compensators, regular maintenance and monitoring are crucial:
Inspect for wear and tear: Regularly examine the compensator for signs of aging, such as cracks, bulges, or degradation of the rubber material.
Clean and protect: Clean the compensator periodically and apply appropriate protective coatings to prevent damage from external elements.
Monitor system performance: Keep an eye on the pipeline system's overall performance, observing for abnormal movements, vibrations, or leaks.
Plan for replacements: Depending on the usage and conditions, schedule periodic replacements to ensure the compensators' optimal functionality.
Safety Considerations: When using rubber compensators, it's important to prioritize safety:
Follow manufacturer guidelines: Adhere to the manufacturer's instructions for installation, maintenance, and replacement procedures.
Use protective gear: Wear appropriate personal protective equipment, such as gloves and safety glasses, when working with rubber compensators.
Seek professional advice: If you're uncertain about any aspect of installation or maintenance, consult with industry experts or professionals.
In conclusion, rubber compensators play a vital role in compensating for thermal expansion, contraction, and misalignment in straight pipelines. By understanding their purpose, installing them correctly, conducting regular maintenance, and prioritizing safety, you can effectively utilize rubber compensators and ensure the smooth operation of your pipeline system.