Installation Considerations for Sleeved Bellow Compensators.
Oct-23-25
Installation Considerations for Sleeved Bellow Compensators. Sleeved bellow compensators, also known as expansion joints, are widely used in piping systems to accommodate expansion and contraction caused by temperature variations, vibrations, and other factors. Proper installation is crucial to ensure the effectiveness and longevity of these compensators. In this article, we will discuss some important installation considerations for sleeved bellow compensators.
Determine the Suitable Type and Size: Before installing a sleeved bellow compensator, it is important to select the appropriate type and size based on your specific application requirements. Consider factors such as the pipe diameter, operating conditions (such as temperature, pressure, and media), and expected movement and vibrations. Consulting with the manufacturer or a qualified engineer can help ensure the right selection.
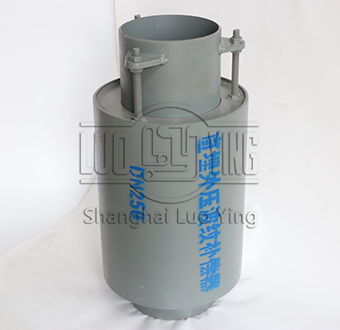
a. Identify the expansion joint location: Determine the ideal position for the compensator installation. It should be placed where the movement is anticipated, such as at bends, offsets, or at the end of long runs.
b. Allow sufficient clearance: Ensure that there is adequate space around the compensator for its movement without any obstruction. The compensator must have ample clearance in both the extended and compressed positions, along with sufficient access for maintenance.
c. Align with pipe connections: Proper alignment of the compensator is critical to avoid undue stress and maintain a leak-tight connection. Align the compensator with the existing pipe connections, ensuring that it is parallel to the pipe axis.
Support and Anchoring: Proper support and anchoring of sleeved bellow compensators are essential to prevent excessive stress and distortion. Consider the following guidelines:
a. Use correct support hardware: Utilize appropriate supports, such as brackets, pipe guides, or hangers, to secure the compensator. Select support materials that are compatible with the compensator material and consider factors like load-bearing capacity and thermal expansion.
b. Allow for movement: The supports should be designed to allow the necessary axial, lateral, and angular movement of the compensator without causing additional stress. Avoid rigid supports that restrict movement or cause bending moments.
c. Consider pipe flexibility: Proper flexibility of the piping system is essential to prevent additional stress on the compensator. Allow for sufficient flexibility in pipe runs near the compensator, using techniques such as expansion loops or pipe offsets.
Quality Installation: To ensure a successful installation, pay attention to the following:
a. Follow manufacturer guidelines: Adhere to the manufacturer's installation instructions and recommended practices. They may provide specific guidelines for assembly, tightening torques, and other critical installation details.
b. Flange alignment and gasket selection: Proper alignment of flanges and selection of suitable gaskets are important for maintaining a leak-tight joint. Ensure that the gaskets are compatible with the fluid and operating conditions, and follow proper bolt tightening procedures.
c. Regular inspections and maintenance: After installation, regularly inspect the compensator for any signs of damage or degradation. Conduct periodic checks on performance, including movement measurements, to identify potential issues and perform timely maintenance.
In conclusion, proper installation of sleeved bellow compensators involves selecting the suitable type and size, ensuring proper positioning and alignment, providing adequate support and anchoring, and following quality installation practices. By considering these installation considerations, you can ensure the effective performance and durability of sleeved bellow compensators in your piping system.