The process of making rubber flexible joints for fans.
Oct-23-26
The process of making rubber flexible joints for fans. Rubber flexible joints are essential components used in fans to minimize vibrations, reduce noise and facilitate smooth operation. These flexible joints are specifically designed to absorb shocks and movements, ensuring the longevity and efficiency of fan systems. In this article, we will explore the process of making rubber flexible joints for fans, highlighting the key steps involved.
Material Selection: The process begins with the careful selection of high-quality rubber materials. Various types of rubber, such as natural rubber, neoprene, or EPDM, may be used depending on the requirements of the fan system. The chosen rubber should possess excellent flexibility, resilience, and resistance to wear, tear, and aging.
Mold Design and Preparation: Once the rubber material is selected, the next step is to design and prepare the mold. The mold acts as a template for shaping and forming the rubber into the desired joint configuration. The mold is typically made from metal or plastic and is precision-engineered to ensure accurate and consistent production.
Rubber Mixing and Compounding: In this step, the selected rubber material is mixed and compounded with various additives to achieve the desired properties. These additives may include vulcanizing agents, fillers, accelerators, and antioxidants. The rubber compound is thoroughly mixed using specialized equipment to ensure uniform distribution of additives and consistent quality.
Molding and Vulcanization: Once the rubber compound is prepared, it is placed into the mold. The mold is then closed and subjected to heat and pressure in a vulcanization process. This process causes the rubber to cross-link and form a solid structure, giving it strength and elasticity. The specific time, temperature, and pressure conditions during vulcanization may vary depending on the type of rubber and the size of the joint.
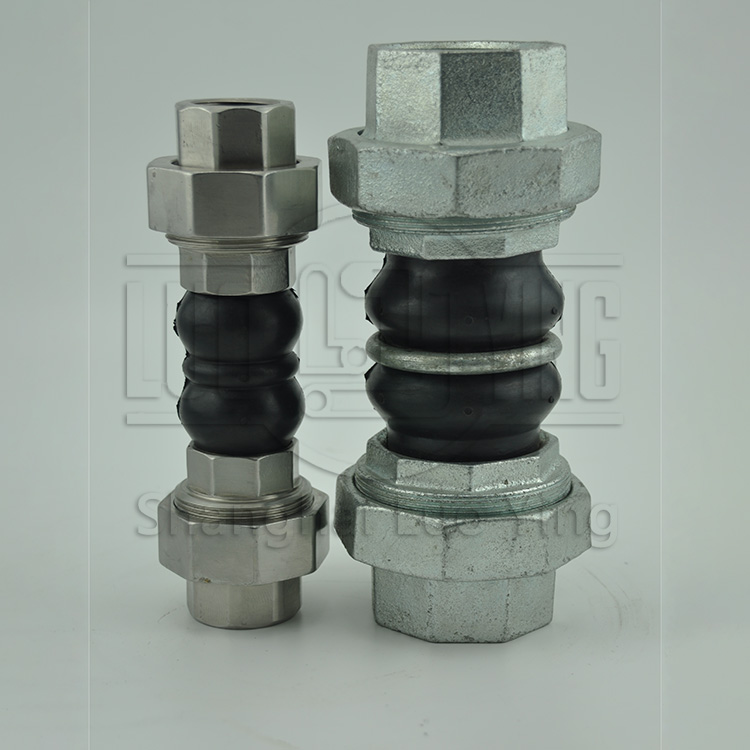
Testing and Quality Assurance: To ensure the reliability and performance of the rubber flexible joint, it undergoes testing and quality assurance procedures. This may include various tests such as dimensional checks, strength testing, and resistance to environmental factors such as temperature and chemical exposure. Only joints that meet the stringent quality standards are approved for use in fan systems.
Packaging and Distribution: Once the rubber flexible joints pass the quality checks, they are carefully packaged and prepared for distribution. The packaging is designed to protect the joints during transportation and storage, ensuring they remain in optimal condition until they are installed in fan systems.
In conclusion, the manufacturing process of rubber flexible joints for fans involves material selection, mold design, rubber mixing and compounding, molding and vulcanization, trimming and finishing, testing and quality assurance, and packaging. Each step is crucial for ensuring the production of high-quality rubber joints that offer excellent flexibility, durability, and performance in fan systems. By absorbing vibrations and reducing noise, these flexible joints contribute to the efficiency and longevity of the fans they are installed in.