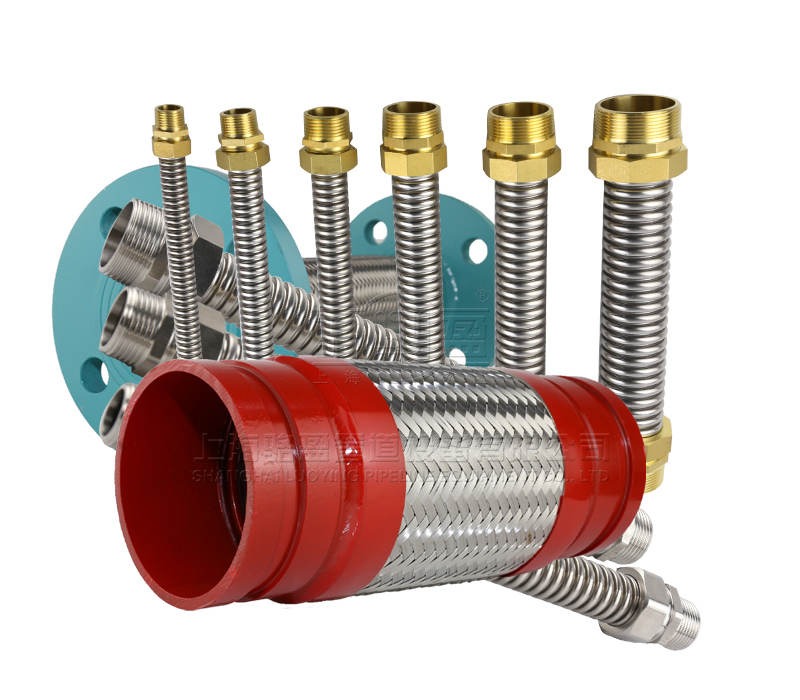
Metal Hoses
Metal hoses are an indispensable part of modern technology with its high demands on piping systems for a wide variety of media and temperatures. High flexibility and highest pressure and temperature resistance characterize our product program and allow their use in many areas, notably in heating, plumbing and air conditioning systems, in the oil and gas industry, in the chemical and food industry, in machine and equipment construction, ship building, railway and automotive engineering.
Reasons for the use of metal hoses rather than a solution with rigid tubes: Stresses in the pipe system Due to stresses in the pipe system may occur - assembly inaccuracies - thermal expansion - vibrations - pressure variations To compensate for these unwanted stresses, a metal hose assembly provides the following advantages: - no pipe ruptures due to fatigue - no leaky flange connections - no difficulty in replacing pipes having been deformed by high temperatures. Savings in assembly/ disassembly - prefabrication of pipes requires less precision - no adjustment work needed on the hose - assembly inaccuracies are easy to correct - only part of the line must be removed - flexible elements are easier to remove and especially to re-install. This results in: - significant savings in assembly and disassembly of pipe systems - higher flexibility in designing the pipe guides and in case of any modifications.
Application:
Steel industryMeasuring and control equipment,Medical equipment,Aviation and space travel,Reactor technologyAlternative energy (solar heat, wind turbines, etc.)
Media:
water, hot water, steam, gas, air, etc.
-
Materials
304L, 316L, and 321 Stainless Steel
-
Size
DN5-300
-
Temp
-270°C to 600°C
-
Pressure
Up to 350bar
Product Range
-
JR Stainless Steel Flanged Metal Hose
This type of hose is also known as pump hose connectors. These hoses are sized to a specific length for attaching to pumps. Its flexible braided construction absorbs vibration to reduce wear and tear on equipment. To connect the pump connector hoses you n
View More
-
304 stainless steel metal hose
Metal hoses are an indispensable part of modern technology with its high demands on piping systems for a wide variety of media and temperatures.
View More
-
JR Netal Flexible Hoses
Flexible Metal hose is a kind of flexible component which is used to conveying different kinds of mediums. It is composed by stainless steel bellow with one or more layers steel thread or steel strip mesh sleeve, two ends with joint or flange head.Stainle
View More
Customized Products
Technical Notes
Manufacturing corrugated hoses
Manufacturing corrugated hoses
The first step in creating a corrugated hose is to shape the starting metal strip from the coil into a smooth, longitudinally welded tube. The strip is continuously welded using the highly precise shielding gas welding method. Then the tube is corrugated by one of the following procedures:
The first step in creating a corrugated hose is to shape the starting metal strip from the coil into a smooth, longitudinally welded tube. The strip is continuously welded using the highly precise shielding gas welding method. Then the tube is corrugated by one of the following procedures:
The mechanical corrugation method, on the other hand, is used to produce both annular and helical corrugated hoses. Usually, multiple profiled pressure rollers are positioned around the tube with an offset that enables them to roll the desired corrugation profile into the tube from the outside to the inside. Both corrugation methods cause material hardening and thus increase the pressure and fatigue resistance of the corrugated hoses.
In addition, corrugated hoses can be manufactured by a special method that is closely related to the manufacture of stripwound hoses. In this procedure, the starting strip is given a corrugated profile in a longitudinal direction. This profile strip is then wound helically and the overlapping coils are tightly welded along the helical seam. After corrugation, the hose may be equipped with a braided sheath (see below). In this case, the hose then passes through a braiding machine that has circumferential wire coil holders, or so-called bobbins.
The wire bundles are wrapped helically around the hose while also being alternately layered one over the other. This creates a tubular braid with the characteristic crisscross pattern. After the fittings are mounted, the hose line is complete. Production-related testing is an integral part of the manufacturing process. It encompasses incoming tests of the starting material as well as dimensional, leakage and pressure testing of the finished conduit.
Flexibility
Bellows
The flexibility of the hose is achieved by means of the elastic behaviour of the corrugation profile. When the hose is bent, the outer corrugations separate while the inner corrugations are squeezed together. The flexibility, bending behaviour and pressure stability of corrugated hoses depend on the selected profile shape. While flexibility increases with an increase in profile height and a decrease in corrugation spacing, pressure resistance decreases. The frequently required semi-flexible bending behaviour is achieved by flat profiles. Depending on the use of the hose, special application-specific profile shapes can be implemented Pressure resistance and flexibility can also be altered by varying the wall thickness. A reduction in the wall thickness increases the bending capacity but reduces the pressure resistance of the hose.
Advantage
Nsure that the hose meets the published levels.-
weight
High physical strength combined with light weight. -
temperature
Suitable for wide temperature range (-2700 C to +7000 C) -
resistance
Good corrosion resistance. -
moisture
Resistance to fire, moisture, abrasion and penetration. -
Compensates
Compensates for intermittent or constant movement. -
Corrects
Corrects problems of misalignment.
Expansion joint accessories
Quality decides value-
Flange
Piping components can be bolted together between flanges. Flanges are used to connect pipes with each other, to valves, to fittings, and to specialty items such as strainers and pressure vessels. A cover plate can be connected to create a "blind flange" Flanges are joined by bolting, and sealing is often completed with the use of gaskets or other methods. Mechanical means to mitigate effects of leaks, like spray guards or specific spray flanges, may be included. Industries where flammable, volatile, toxic or corrosive substances are being processed have greater need of special protection at flanged connections. Flange guards can provide that added level of protection to ensure safety.
-
Covers
Fasteners are used for fastening and securing materials such as wood, metal, plastic, or concrete. They include nuts and bolts, threaded rods, structural bolts, machine screws, wedge anchors, washers, rivets, and more in a variety of types and sizes, including metric and inch.
-
Particulate barriers/purge connectors
In systems that have a media with significant particulate content (i.e. flash or catalyst), a barrier of ceramic fiber can be utilized to prevent corrosion and restricted bellows flexibility resulting from the accumulation of the particulate. Purge connectors may also be utilized to perform this same function. Internal liners must also be included in the design if the expansion joint includes purge connectors or particulate barriers.
-
Liners
A gasket is a mechanical seal which fills the space between two or more mating surfaces, generally to prevent leakage from or into the joined objects while under compression. It is a deformable material that is used to create a static seal and maintain that seal under various operating conditions in a mechanical assembly.