Production process of buried corrugated compensator and its characteristics introduction
Feb-23-16
Buried corrugated compensator should be sealed to prevent pollution. Clean the pipeline and the buried corrugated compensator to prevent dropping iron oxide scale and other debris. Clean with lint-free cloth or special paper. Twine and adhesive shall not be used to seal the buried corrugated compensator. According to the design requirements, pay attention to the change of oil temperature and oil pressure. When no load, unscrew the exhaust bolt for exhaust. The buried corrugated compensator pipeline connection shall not be loose, and the base of buried corrugated compensator shall have sufficient rigidity, otherwise the cylinder barrel will bend upward during the pressurization process, making the piston rod bend.I. Production process.
Before installing the buried corrugated compensator into the system, the parameters on the label of the buried corrugated compensator should be compared with those on the order. For foot-fixed moving cylinders, the shaft should be concentric with the line of the load force to avoid lateral forces that can easily wear the seals and damage the piston. When installing the in-ground corrugated compensator for moving objects, the in-ground corrugated compensator should be made parallel to the direction of movement of the moving object on the surface of the guide rail, and its parallelism should generally be no more than 0.05mm/m.
The degree of tightening should ensure that the piston moves flexibly throughout the stroke, without stalling and uneven weight. If the screw is tightened too much, it will increase the resistance and accelerate the wear; too loose will lead to oil leakage. Many steps will be taken in the processing of the buried corrugated compensator to obtain a pipe with such high performance. Elimination of process hardening of cold drawn steel pipe can obtain satisfactory metallographic organization. Process equipment is bright annealing furnace, mainly used for heat treatment of stainless steel products in a protective atmosphere.
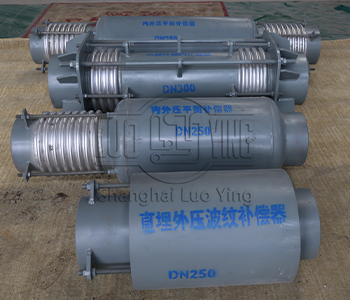
When the application performance requirements of the buried corrugated compensator are different, the metallurgical organization requirements after bright annealing are different, so the bright heat treatment process will be different. After cold working, buried corrugated compensator buried corrugated compensator in the ground will leave residual stress, which is very detrimental to the anti-stress corrosion cracking performance of the pipeline. Any degree of cold working will result in a significant increase in the susceptibility of the buried corrugated compensator to stress corrosion cracking.
The degree of cold working can also adversely affect the high temperature lasting strength of austenitic stainless steel. The higher the operating temperature or the higher the fracture life requirement, the lower the degree of cold working. Another important issue in the heat treatment of pipes for buried corrugated compensators is the requirement for a uniform structure across the width and length of the pipe. The buried corrugated compensator uses a large size muffle tube to evenly organize the heating airflow outside the buried corrugated compensator in the future and rotate around the furnace so that the pipe is evenly heated.