Wear-resistant rubber joint inner rubber formula design, and rubber vulcanization system
Feb-23-20
When the pipeline produces instantaneous pressure and is greater than the working pressure, the joint with a gear higher than the working pressure should be selected. When the pipeline medium is acid and alkali, oil, high temperature and other special materials, the joint with higher than the working pressure of the pipeline should be selected. The use or storage of wear-resistant rubber joints should avoid high temperature, ozone, oil and acid-alkali environment. Outdoor or sunny pipelines should be set up with shade shelves, and exposure, rain and wind erosion are strictly prohibited.
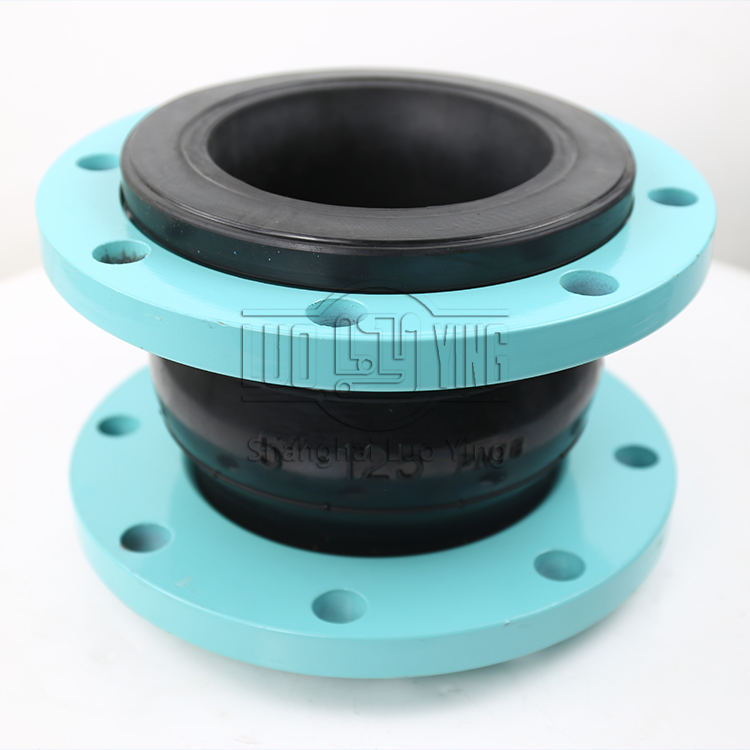
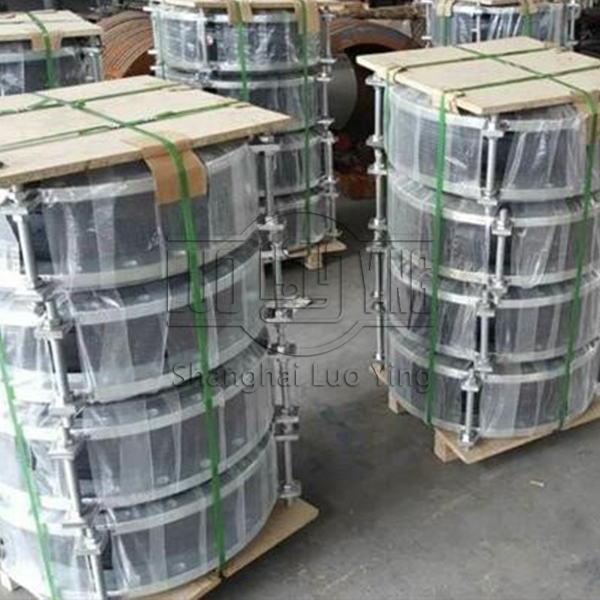
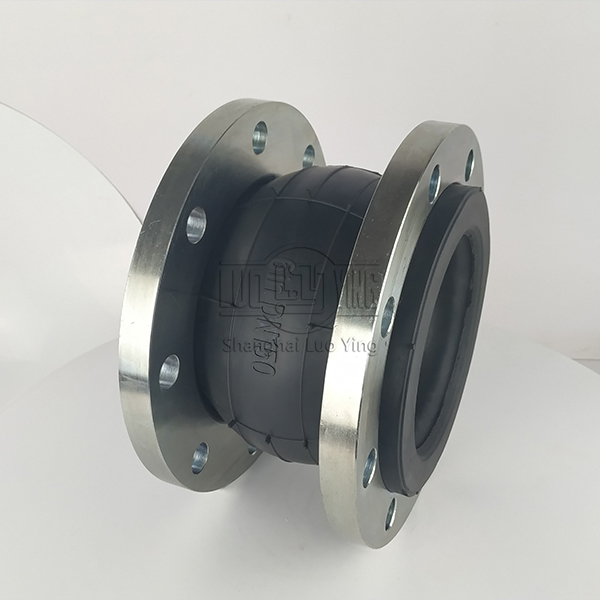
The joints are dense and good, especially the high-pressure hose that conveys gas. Good adaptability compared to the transported medium. For example, oil hose requires swelling resistance, chemical hose requires corrosion resistance, precipitation hose requires wear resistance, food hose requires non-toxic and odorless. When restarting under pressure or for a long time, the bolts should be re-pressurized and tightened, and then put into operation. The quality of inner rubber of wear-resistant rubber joints depends on the requirements of flexible rubber joint design for inner rubber. The normal applicable medium of wear-resistant rubber joints is 0-6000℃ ordinary water, oil, acid and alkali, high temperature and other special mediums with corrosive and hard texture should choose the corresponding special durable material rubber joints, and should not be blindly connected in series or general purpose. Screw joints should be tightened evenly with a standard wrench. Do not slide, slide or break the live joint with a stiffener, and check regularly to avoid loosening or water seepage. The inner rubber formulation design is a working surface for conveying medium and a part with harsh usage conditions.
Abrasion-resistant rubber joint formulations are designed with rubber types mainly natural rubber and SBR, or natural rubber, SBR and rubber; they can also be mixed with rubber and plastic, or moderate amounts of recycled rubber. Industrial applications include rubber joints and flexible rubber joints with a typical rubber content of 25 to 30 percent. conventional vulcanization systems are typically used for vulcanization and accelerators. Vulcanization doses of 1.5 to 2.0 thiazole and sulfonamide accelerators are more effective. Abrasion-resistant rubber joints have a certain degree of elasticity, flexibility and aging resistance. Semi-finished products have sufficient hardness, small shrinkage, compression, smooth calendering surface and easy molding and other process processing requirements.