Performance characteristics of double-layer bellows compensator
Jun-23-02
Performance characteristics of double-layer bellows compensatorDouble-layer bellows compensator is resistant to high pressure and high temperature: the shell wall of the multi-layer metal bellows compensator is composed of a cylinder made of multiple layers of thin plates rolled and welded together. Before assembly, the surface of each layer should be kept clean, the surface between the layer and the layer should be closely fitted, no looseness and wrinkles, the gap between each layer should not exceed 0.1mm-0.3mm, the circumferential gap should be uniform, and the longitudinal welds of each layer should be evenly staggered with each other.
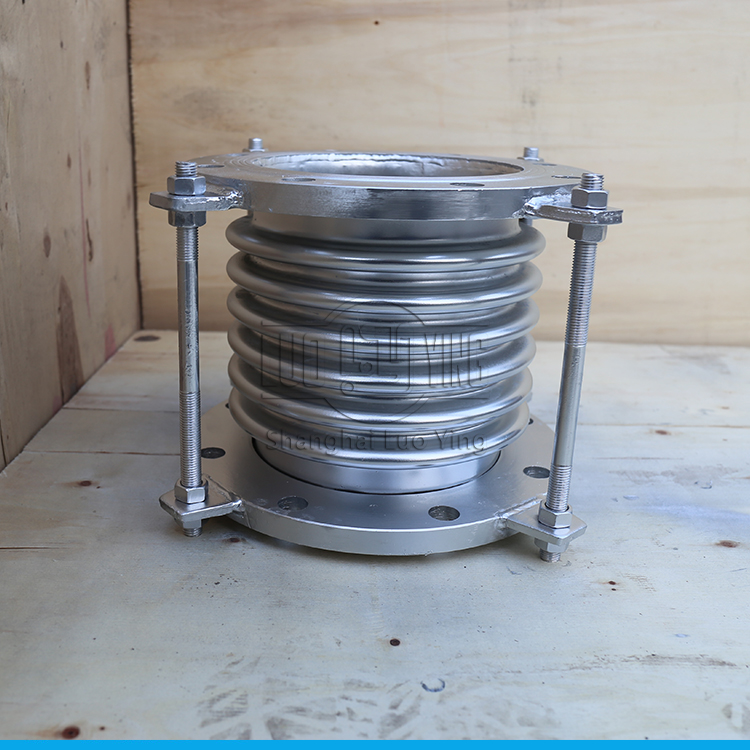
1, positioning brace height: the distance along the axial direction of the outer wall of the pipe billet is approximately equal to the length of the single wave unfolded as the height of the positioning brace.
2, reinforced bellows compensator: can be molded with the outer reinforcement ring to play the role of the mold. After forming and demoulding, the ring becomes an integral part of the bellows.
3、Moving speed of hydraulic press: moving too fast, poor molding quality, large rebound, easy to produce scrap; if too slow, the production efficiency will be low. Generally, the moving speed of hydraulic press should be controlled according to the material characteristics and the structure of the bellows.
4. Pay attention to whether the Y-seal is damaged. If the position of the positioning support deviates during the molding process, the deviation should be corrected immediately to ensure the molding quality.
5、The liquid discharge should be synchronized with the horizontal movement of hydraulic pressure. As the hydraulic press moves, the volume of the pipe billet gradually becomes smaller and the excess liquid must be discharged accordingly with the downward movement of the hydraulic press. Synchronization control is often achieved by installing a relief valve in the hydraulic system and carefully adjusting the pressure of the relief valve so that the oil pressure remains constant throughout the forming process.
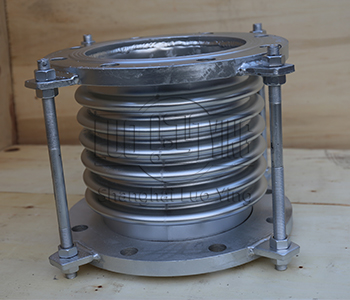