Winding process and method of rubber expansion joints.
Jul-23-28
Winding process and method of rubber expansion joints. The winding process and method of rubber expansion joints is a crucial aspect of their manufacturing. Rubber expansion joints, also known as rubber bellows, are flexible connectors used in piping systems to accommodate movements, vibrations, and thermal expansion. In this essay, we will explore the winding process and method used to manufacture rubber expansion joints.
Material Selection: The first step in the winding process is selecting the appropriate rubber material. Commonly used rubber materials for expansion joints include EPDM (Ethylene Propylene Diene Monomer), Neoprene, Nitrile, and Natural Rubber. Each material has specific properties such as temperature resistance, chemical compatibility, and flexibility, which determine its suitability for different applications.
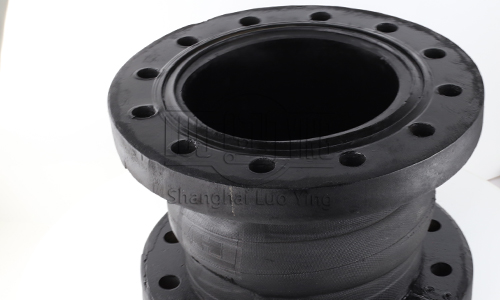
Reinforcement: To enhance the strength and durability of the expansion joint, reinforcement materials are incorporated into the design. Reinforcement options include various fabrics such as polyester, nylon, or aramid, as well as metal wire or rings. These reinforcements are inserted between the rubber layers during the winding process to provide additional tensile strength and support.
Winding Technique: The winding technique is a critical aspect of the manufacturing process. The rubber material is wound tightly around the mandrel or form in a specific pattern to create a seamless and uniform expansion joint. The winding is done in a helical or spiral pattern to ensure even thickness and distribution of rubber material throughout the joint. This winding technique ensures the joint's flexibility and ability to accommodate movements without causing stress or strain on the system.
Vulcanization: After completing the winding process, the rubber layers are vulcanized to bond them together and create a strong, resilient expansion joint. Vulcanization involves subjecting the joint to high heat and pressure in a vulcanizing press. This process activates chemical reactions in the rubber material, causing it to crosslink and form a solid, durable structure. The time and temperature of vulcanization may vary depending on the specific rubber material used.
Finishing: Once the vulcanization is complete, the rubber expansion joint undergoes finishing processes. These processes typically involve trimming off excess rubber, removing the mandrel or form, and inspecting the joint for any defects. The finished expansion joint may also undergo additional testing, such as pressure and leak tests, to ensure its functionality and reliability.
In conclusion, the winding process and method of rubber expansion joints play a significant role in their manufacturing. The selection of appropriate rubber materials, the winding technique, incorporation of reinforcements, and vulcanization process contribute to the integrity, strength, and flexibility of the expansion joint. The expertise and precision employed in the winding process ensure that the finished product meets the required specifications and performs effectively in various piping system applications.