What is the basis for the selection of the grooved wear-resistant rubber joint?
Feb-23-08
In all welding applications of grooved wear-resistant rubber joints, the edges of the grooved wear-resistant rubber joints are melted, and when the clamping brackets are used to knead the edges of the grooved wear-resistant rubber joints together, the edges are condensed. However, the nature of laser welding is that it has a high energy beam density. The laser beam not only melts the surface layer of the material, but also creates a keyhole, resulting in a narrow weld profile. With power densities below 1 MW/cm2, such as the GTAW technique, the energy density is not sufficient to produce a keyhole.As a result, a keyhole-free process yields a wide and shallow weld profile. The high precision of laser welding brings higher power penetration, which in turn reduces grain growth and brings better metallurgical quality; on the other hand, the higher heat input of GTAW with slower cooling process leads to a rough weld structure. In the welding of the grooved wear-resistant rubber flexible joint plant, the welding is determined by the thickness of the grooved wear-resistant rubber flexible joint. In this way, the production policy is to advance formability by reducing the welding width, while achieving higher speeds. When selecting the appropriate laser, one must consider not only the beam quality, but also the accuracy of the grooved wear-resistant rubber joint.
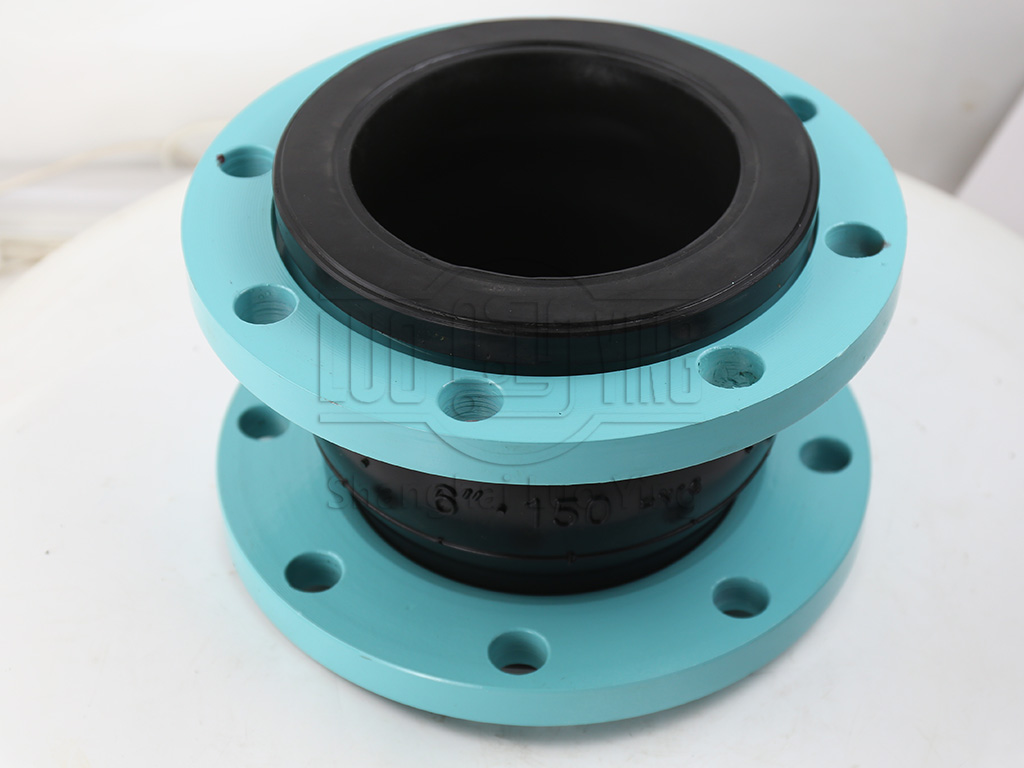
Too much pressure will result in excess material at the top or perhaps the inside diameter of the grooved abrasion resistant rubber joint. On the other hand, severe and perhaps minor welding misalignment will result in poor weld profile. After passing through the welding box, the grooved wear-resistant rubber joint will be further trimmed. This includes scale adjustments and shape (form) adjustments. On the other hand, additional work can remove some serious/minor welding faults, but perhaps not all of them. Of course, we want to achieve zero defects. Generally speaking, the rule of thumb is not to exceed five percent of the thickness of the material. Exceeding this value will affect the strength of the welded product.